Japanese Companies Seeking a Way Out Amid Shrinking Domestic Demand Through Functional and Eco-Friendly Materials
Publish date: 2025-02-12
Japan's plastics industry is focusing on environmental initiatives to drive business development. While efforts are being made to promote energy-saving measures in production processes, recycling, and the development of bioplastics, global demand is soaring to unprecedented levels. Manufacturers are finding it increasingly difficult to cope with the current situation, placing their survival at risk.

Japan is exploring the restructuring of petrochemical joint ventures.
(Keiyo Region: Home to Japan's largest ethylene production capacity)
(Keiyo Region: Home to Japan's largest ethylene production capacity)
Declining Production and Severe Competition
In fact, Japan's plastic production is experiencing a significant decline. According to a summary by the Japan Plastics Industry Federation, the country’s plastic production in 2023 was 8.79 million tons, a nearly 20% decrease compared to a decade ago. Except for an 18% increase in plastics used for transportation equipment, primarily in the automotive sector, all other categories showed a downward trend. The decline was particularly notable in sheets and pipes, which dropped by over 30%, while films, construction materials, household goods, and miscellaneous items decreased by more than 10%.
In neighboring China, the production of all types of plastics is growing rapidly, with aggressive export strategies targeting overseas markets. As a result, Japan's plastics industry is at a disadvantage in terms of scale and cost competitiveness, gradually losing its presence in the mass consumer goods market. Moreover, discussions are underway in Japan regarding the restructuring of ethylene production facilities, which is expected to further reduce the output of all chemical products. To navigate these challenges, Japanese manufacturers need to focus on enhancing functionality and adopting eco-friendly materials.
In neighboring China, the production of all types of plastics is growing rapidly, with aggressive export strategies targeting overseas markets. As a result, Japan's plastics industry is at a disadvantage in terms of scale and cost competitiveness, gradually losing its presence in the mass consumer goods market. Moreover, discussions are underway in Japan regarding the restructuring of ethylene production facilities, which is expected to further reduce the output of all chemical products. To navigate these challenges, Japanese manufacturers need to focus on enhancing functionality and adopting eco-friendly materials.
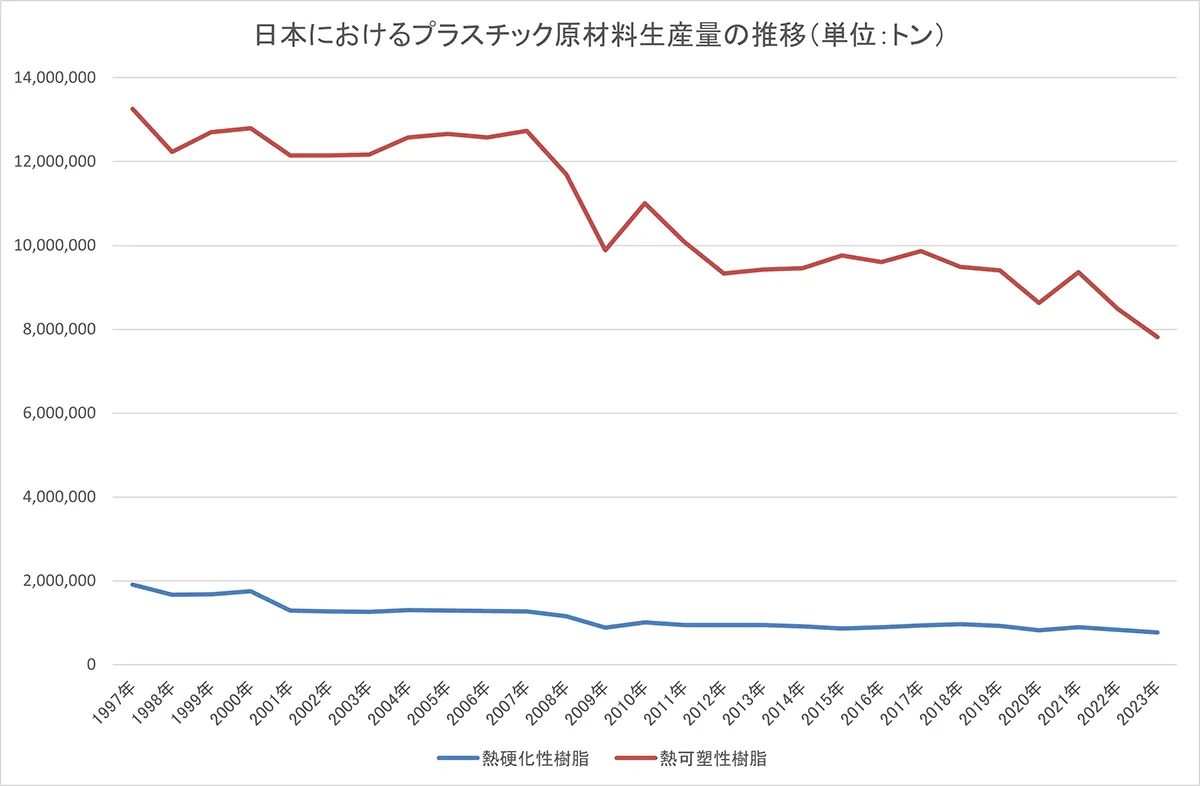
Plastic raw materials production in Japan (unit: tons)
(Source: The Japan Plastics Industry Federation)
(Source: The Japan Plastics Industry Federation)
Increasing Demand for Recycled Plastics and Eco-friendly Materials
The demand for eco-friendly materials among plastics users is rising steadily. To enhance consumer appeal, there has long been a trend of using recycled plastics in certain components of home appliances and office automation (OA) equipment. Currently, as part of Corporate Social Responsibility activities by machinery manufacturers, the OA industry is heavily promoting environmental awareness. The Home Appliance Recycling Law enacted in 2001 mandates the use of eco-friendly materials in the home appliance sector.
In the automotive industry, in light of Europe’s implementation of the End-of-Life Vehicle (ELV) directive, which requires the use of recycled plastic products in vehicles, Japanese manufacturers have solidified their stance on mastering advanced utilization technologies and establishing supply chains. To support the goal of using recycled plastics in 25% of total vehicle plastics, including 6.25% car-to-car recycled plastic, polypropylene (PP) is the initial focus. However, a comprehensive recycling system is necessary for all resin materials, including polyamides (PA), polybutylene terephthalate (PBT), and polyphenylene sulfide (PPS), as merely relying on PP and meeting the required recycling volumes remains unfeasible.
To further advance a circular economy in the automotive sector, Toyota established the non-profit organization "Circular Core" in October 2024, initiating the development of a mechanism to recover plastics and metals from end-of-life vehicles for reuse in new cars. Additionally, in July of the same year, a group led by waste plastic recycling companies formed the "Sustainable Plastics Initiative" to expand the use of recycled plastics. Toyota also played a key role in this initiative, with its personnel serving as secretary-general. The organization is actively building systems to collect and allocate funds for the production of recycled resin components.
“Japan's Resource Circulation Strategy for Plastics” formulated in 2019, set a target of introducing approximately 2 million tons of bioplastics by 2030. In addition to biomass plastics such as polybutylene succinate (PBS) and polyhydroxyalkanoates (PHA), there has been a growing adoption of the mass balance approach, which allocates biomass content according to customer demands. Many material manufacturers have obtained ISCC PLUS certification and are working to accelerate the adoption. However, challenges remain, including the time required to educate end consumers with the concept of mass balance and the high cost of raw materials such as bio-naphtha.
In the automotive industry, in light of Europe’s implementation of the End-of-Life Vehicle (ELV) directive, which requires the use of recycled plastic products in vehicles, Japanese manufacturers have solidified their stance on mastering advanced utilization technologies and establishing supply chains. To support the goal of using recycled plastics in 25% of total vehicle plastics, including 6.25% car-to-car recycled plastic, polypropylene (PP) is the initial focus. However, a comprehensive recycling system is necessary for all resin materials, including polyamides (PA), polybutylene terephthalate (PBT), and polyphenylene sulfide (PPS), as merely relying on PP and meeting the required recycling volumes remains unfeasible.
To further advance a circular economy in the automotive sector, Toyota established the non-profit organization "Circular Core" in October 2024, initiating the development of a mechanism to recover plastics and metals from end-of-life vehicles for reuse in new cars. Additionally, in July of the same year, a group led by waste plastic recycling companies formed the "Sustainable Plastics Initiative" to expand the use of recycled plastics. Toyota also played a key role in this initiative, with its personnel serving as secretary-general. The organization is actively building systems to collect and allocate funds for the production of recycled resin components.
“Japan's Resource Circulation Strategy for Plastics” formulated in 2019, set a target of introducing approximately 2 million tons of bioplastics by 2030. In addition to biomass plastics such as polybutylene succinate (PBS) and polyhydroxyalkanoates (PHA), there has been a growing adoption of the mass balance approach, which allocates biomass content according to customer demands. Many material manufacturers have obtained ISCC PLUS certification and are working to accelerate the adoption. However, challenges remain, including the time required to educate end consumers with the concept of mass balance and the high cost of raw materials such as bio-naphtha.
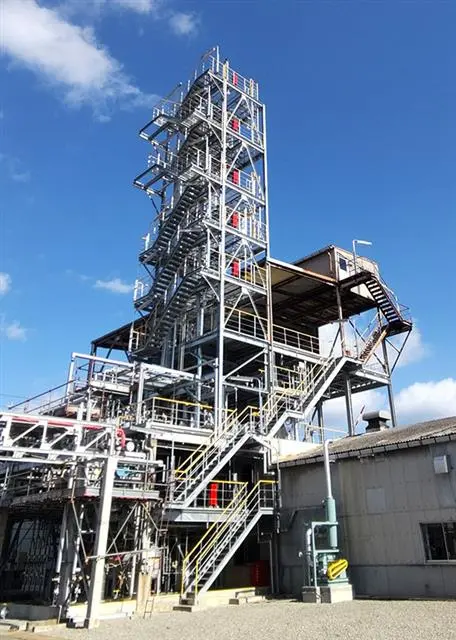
Sumitomo Chemical's PMMA resin chemical recycling demonstration equipment at its Ehime plant
Technology Development and New Application Exploration
Like overseas manufacturers, Japanese plastics producers are advancing technology development and exploring new applications in both mechanical recycling and chemical recycling. In the area of chemical recycling, various technologies are being developed and tested, ranging from methods targeting specific plastics to technologies that convert mixed or composite plastics into oil. By the 2030s, chemical recycling could become a game changer, potentially transforming the structure of the petrochemical industry. Efforts are already underway to establish trial equipment for polystyrene (PA) and acrylic resins, and in the fiber sector, the use of PA and polyester fibers is expanding.
Toray has been developing chemical recycling products for over 20 years. They process edge material produced during manufacturing by depolymerizing and repolymerizing it to create PBT, working to expand and enhance its functional grades.
There are many obstacles to recycle engineering plastics, such as the presence of alloys with other plastics, various additives like reinforced fillers, and bonding with different materials like metals. However, multiple technologies are being employed to address these challenges, such as using recycled materials in alloyed materials, depolymerization using subcritical water, and separation technologies for multilayer films, all aimed at achieving a circular society. Mitsubishi Chemical Group and ENEOS have jointly introduced oil-based recycling equipment in Ibaraki Prefecture, with an annual waste plastic processing capacity of 20,000 tons. In the second half of 2025, Idemitsu Kosan will launch its first unit at a neighboring area of its Chiba plant, with an annual waste plastic processing capacity of 20,000 tons.
Toray has been developing chemical recycling products for over 20 years. They process edge material produced during manufacturing by depolymerizing and repolymerizing it to create PBT, working to expand and enhance its functional grades.
There are many obstacles to recycle engineering plastics, such as the presence of alloys with other plastics, various additives like reinforced fillers, and bonding with different materials like metals. However, multiple technologies are being employed to address these challenges, such as using recycled materials in alloyed materials, depolymerization using subcritical water, and separation technologies for multilayer films, all aimed at achieving a circular society. Mitsubishi Chemical Group and ENEOS have jointly introduced oil-based recycling equipment in Ibaraki Prefecture, with an annual waste plastic processing capacity of 20,000 tons. In the second half of 2025, Idemitsu Kosan will launch its first unit at a neighboring area of its Chiba plant, with an annual waste plastic processing capacity of 20,000 tons.
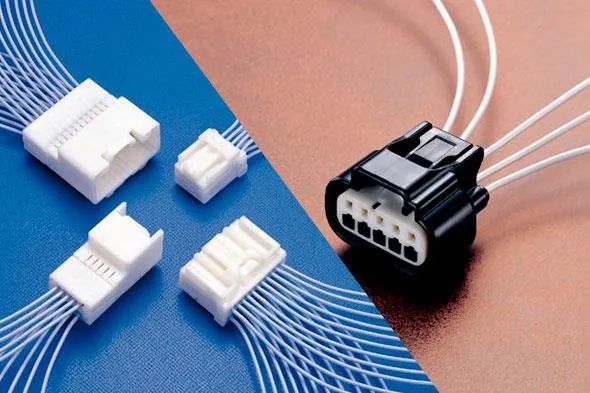
Toray Aims to Develop Connectors for Automotive Wire Harnesses Using Recycled PBT Resin
On the other hand, with the development of automotive electrification, the use of engineering plastics is expanding. There is a growing demand for materials that replace metals to achieve light-weighting without compromising properties such as heat resistance, strength, and rigidity, as well as materials with insulation and flame-retardant properties for high-voltage battery areas. A trend is emerging where thermosetting resins and engineering plastics are used to replace metals around vehicle battery housings. It is necessary to design materials that are easy to disassemble during material conversion and disposal, and resin producers must address these design and material demands. In terms of recyclability, rapid progress is being made in developing uniform component materials for food packaging.
At CHINAPLAS 2025, the event will showcase comprehensive application solutions for plastics. Japanese plastics manufacturers can gain insights into the latest developments of Japanese enterprises and global chemical companies, as well as cutting-edge trends in the industry. This will drive the plastics sector towards a more sustainable and resilient future. For more information, visit: www.chinaplasonline.com.
At CHINAPLAS 2025, the event will showcase comprehensive application solutions for plastics. Japanese plastics manufacturers can gain insights into the latest developments of Japanese enterprises and global chemical companies, as well as cutting-edge trends in the industry. This will drive the plastics sector towards a more sustainable and resilient future. For more information, visit: www.chinaplasonline.com.
About CHINAPLAS 2025
CHINAPLAS 2025, one of the world’s most prestigious international plastics and rubber trade fairs, will be held at Shenzhen World Exhibition & Convention Center (Bao’an), PR China on April 15-18, 2025. The exhibition will bring together 4,300 international exhibitors under one roof and welcome visitors from across the globe, providing unmatched opportunities to explore the latest innovations and forge valuable connections.
The online pre-registration of CHINAPLAS 2025 has started. Pre-register NOW for an admission ticket at RMB 50 or USD 7.5. Pre-registered visitors shall receive their Visitor eBadges (for local visitors) or eConfirmation Letters (for overseas visitors). Admission tickets are available on a first-come, first-served basis.
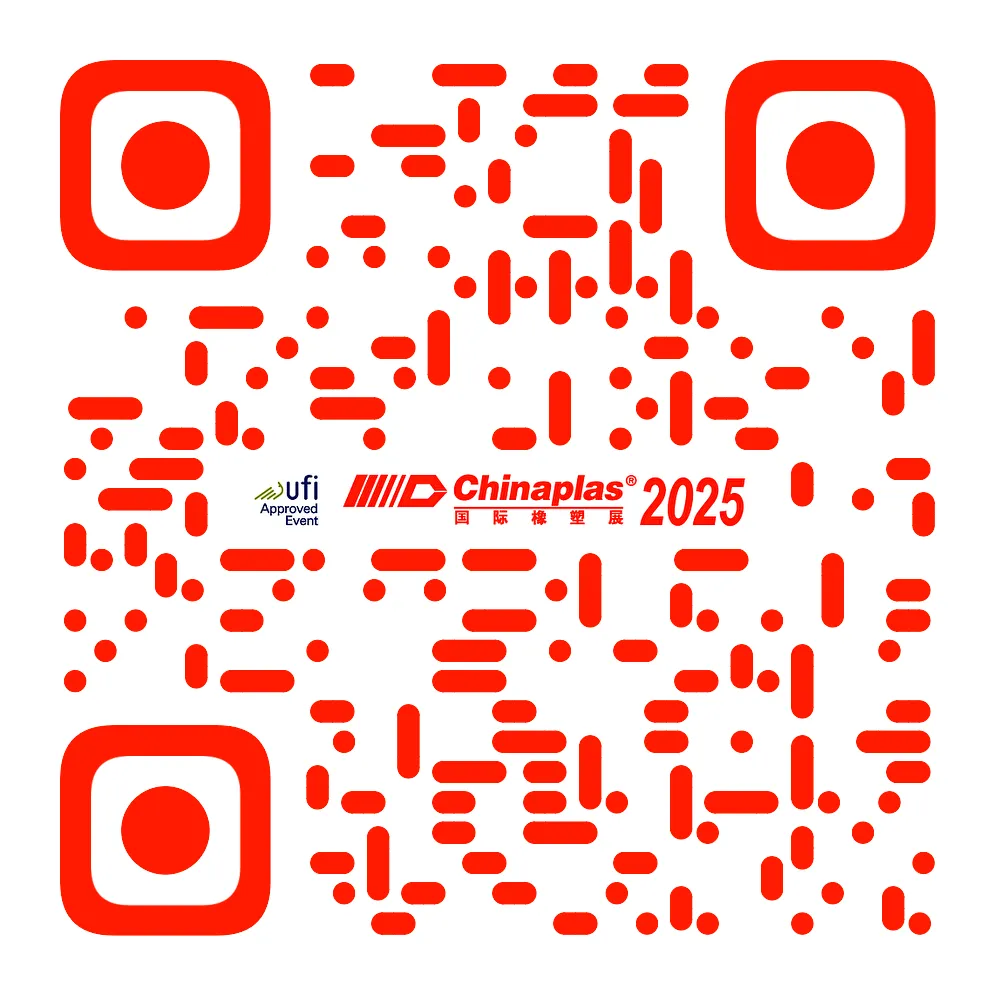
Besides the show days, the exhibition also enables buyers to connect with thousands of materials and machines suppliers all year round via CPS+ eMarketplace, a smart efficient integrated, and sustainable online sourcing platform which is complementary to the physical show of CHINAPLAS.
For more information, please visit: www.ChinaplasOnline.com.
CHINAPLAS 2025, one of the world’s most prestigious international plastics and rubber trade fairs, will be held at Shenzhen World Exhibition & Convention Center (Bao’an), PR China on April 15-18, 2025. The exhibition will bring together 4,300 international exhibitors under one roof and welcome visitors from across the globe, providing unmatched opportunities to explore the latest innovations and forge valuable connections.
The online pre-registration of CHINAPLAS 2025 has started. Pre-register NOW for an admission ticket at RMB 50 or USD 7.5. Pre-registered visitors shall receive their Visitor eBadges (for local visitors) or eConfirmation Letters (for overseas visitors). Admission tickets are available on a first-come, first-served basis.
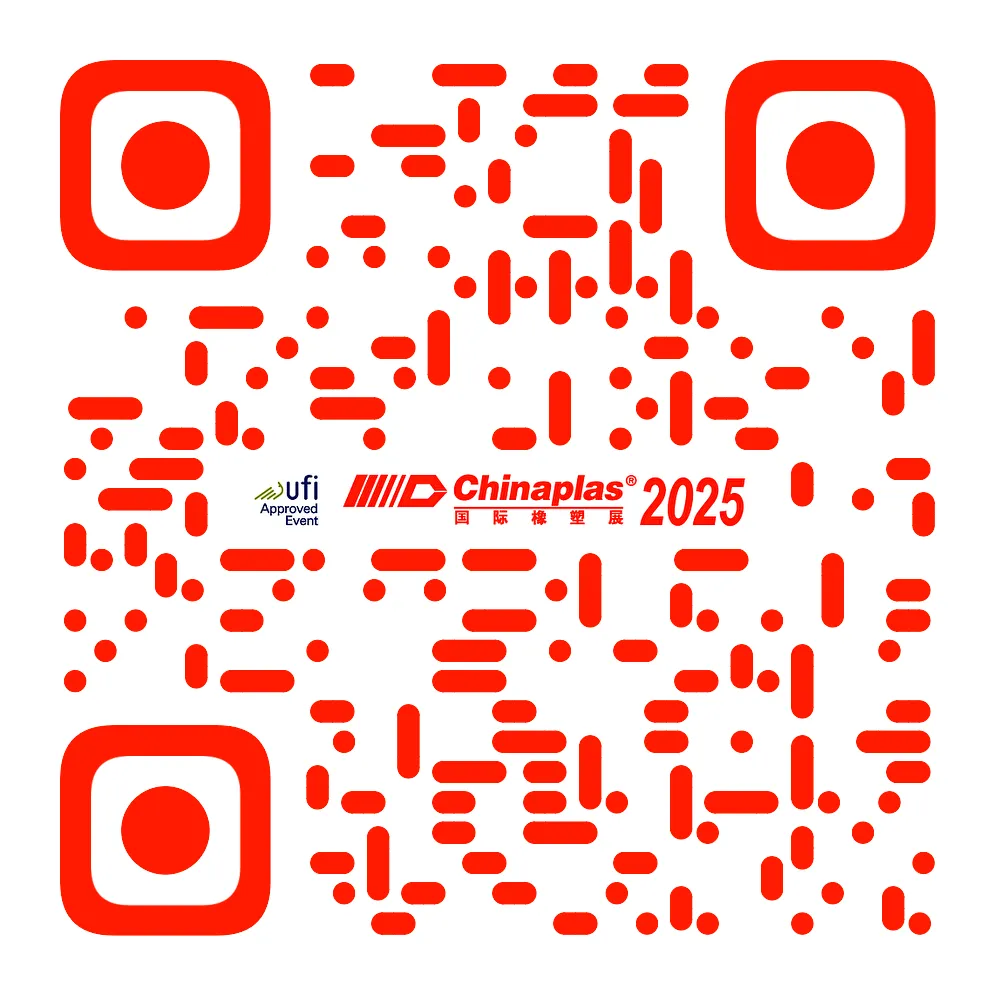
Scan to pre-register
Besides the show days, the exhibition also enables buyers to connect with thousands of materials and machines suppliers all year round via CPS+ eMarketplace, a smart efficient integrated, and sustainable online sourcing platform which is complementary to the physical show of CHINAPLAS.
For more information, please visit: www.ChinaplasOnline.com.